Thomas Menke moved into Northeast Minneapolis the week of 911. Big changes were afoot for him in 2001 as he was leaving his 20-year career as a graphic designer to become a furniture maker.
His studio journey began in the Thorpe building. After 10 years he moved to the Northrup King Building. Seeking more square footage, he transferred to the Casket Arts Building Annex. Menke’s home and identity remain in Northeast, though his studio is just outside the Arts District. He also uses the maker space MPLS MAKE in Columbia Heights.
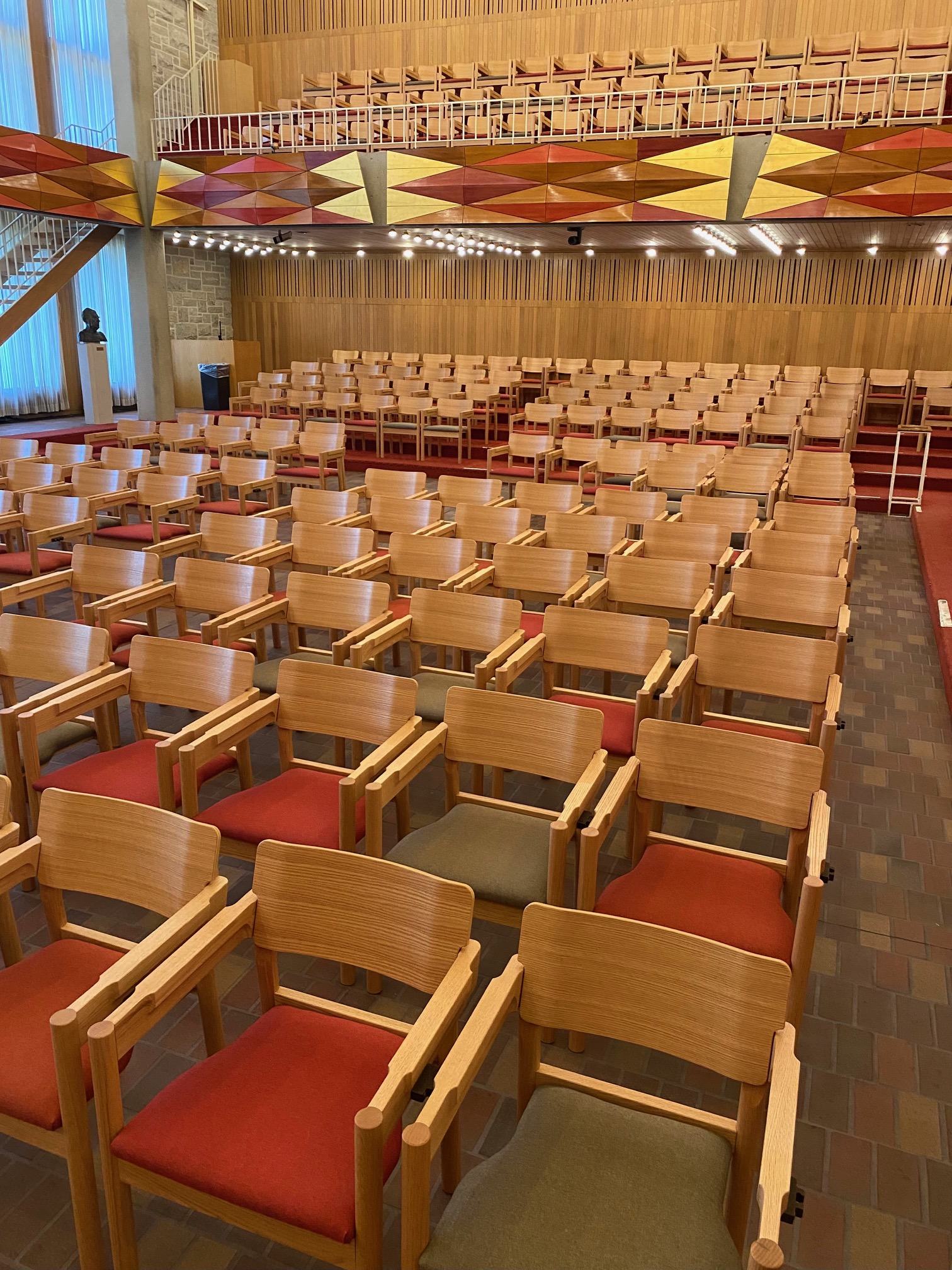
Menke describes himself as a Furniture Designer/Maker. A commission by St. Olaf College in Northfield catapulted him into new territory as a woodworker. They needed to replace 300 chairs in their recital hall. We talked about how this project has changed his pursuit. Is he a one-of-a-kind maker or handmade production designer and maker? Is he a craftsman or an artist? These are always questions artisans grapple with as their practice grows. New opportunities often push a maker’s technical capabilities, and also their identity.
Interior Designer Ariane Laxo of HGA Architects contacted Menke to submit for the project. HGA was tasked with a remodel of Urness Recital Hall in the Christiansen Hall of Music at St. Olaf College. By coincidence he had built a credenza for Ariane several years earlier. She remembered Tom’s work.
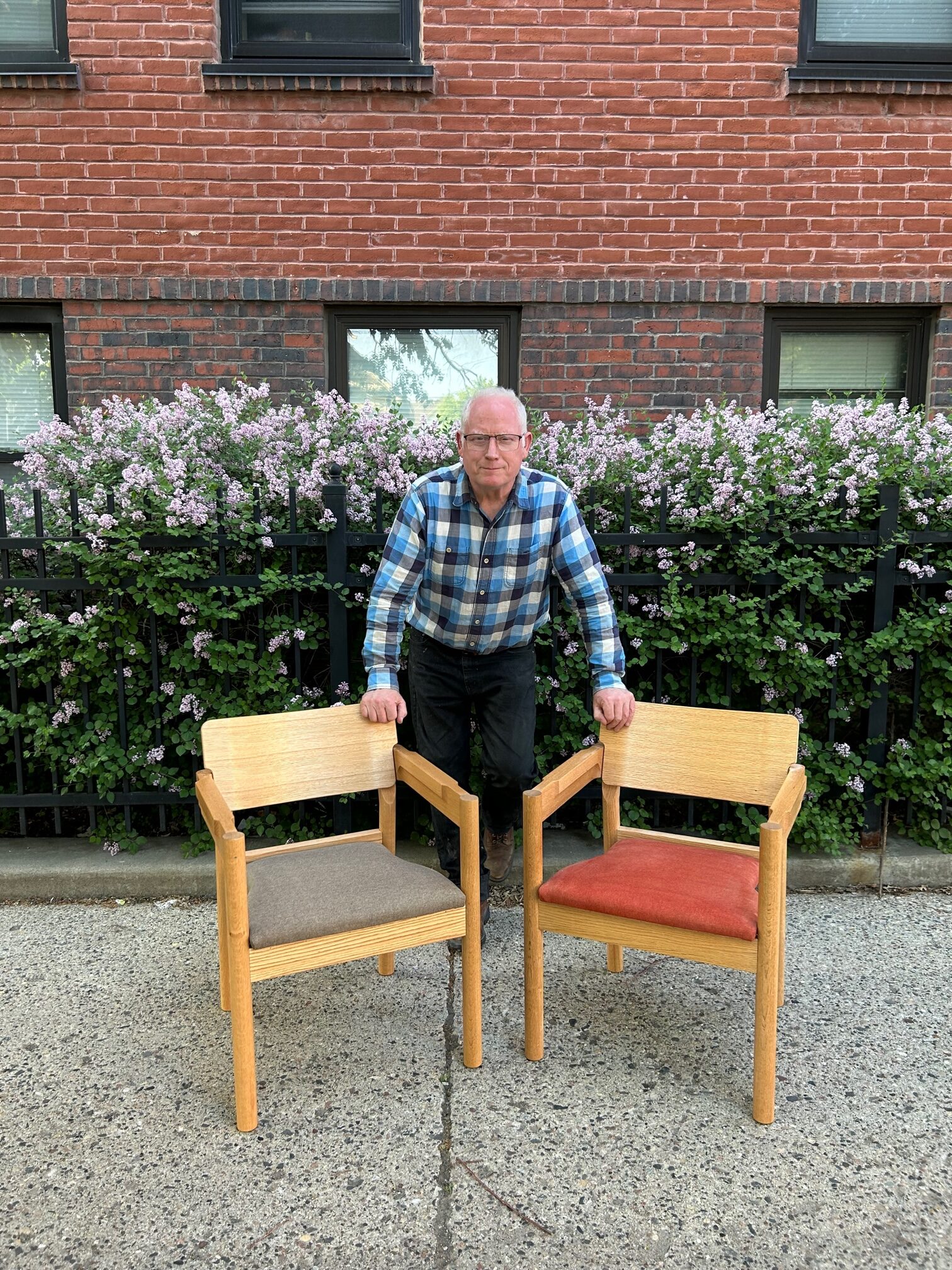
Updating the existing recital hall chair from the mid-1970’s posed design challenges. St. Olaf desired seating that supported a more upright position instead of the existing lounge-like chair. Chairs had to stack to accommodate different seating arrangements. The original chair also had serious wear issues.
Menke found himself in competition with a proposal to reconfigure the existing chair. Tom’s proposal was for the design and build of a completely new chair. Menke’s design raised the seat height and used a curved wood back with a padded seat. In the end, his design won over the St. Olaf project committee.
The 18-month project involved 6 months of prototyping and 12 months of fabrication and assembly. Menke made two Alpha prototypes of stackable chairs for the first design review. Then he made six more to refine the design and achieve a successful Beta version. This design was the test for the entire process. After moonlighting with a CNC guy (Computer Numerical Control – a digital technology), he bought a CNC machine and other larger machines for the project.
He had hired a handful of helpers to produce the parts. “First month we focused on building seats. Second month, the front leg, and so on for the other parts. We built 300 parts, then the next 300 parts, and stored them for assembly later,” Menke said.
Menke had to apply production thinking rather than one-of-a-kind or short run methods. He was not building each chair one by one, but he had to make precise, interchangeable parts. All of the parts had to fit together at the end, which he said they did flawlessly. The extra time in refining the prototypes made the assembly of the 300 chairs an enjoyable experience.
Tom Menke distinguishes himself as a Designer/Maker, and is choosing not to compete with design teams in larger firms who don’t directly produce what they design. He’s looking at other opportunities like this to become a bigger designer maker, or even a branded maker.
But that requires a big leap. It requires him to hire staff which would be a big change. He is contemplating his next move and where he wants to go.
— by Josh Blanc